Содержание:
- Историческая справка
- Как работают сборочные линии автомобилей
- Кто первым использовал автоматизированную сборную линию
- Современная производственная линия
- Автомобильная платформа как элемент стандартизации
- Завод Hyundai: роботы и ИИ на службе человека
- Как производится Porsche: один из самых современных заводов в мире
- Кузовной цех
- Покрасочный цех
- Этап "свадьбы"
- Тестовая линия
- Как производят электромобили: самое интересное о Fiat 500 electric
- Как работает завод Mirafiori: инновации, роботы
Об истории создания электромобилей Liga.Tech уже писала раньше. В этом материале поговорим о процессе производства современных автомобилей. А именно – как выглядит современная производственная линия, как можно заказать автомобиль с помощью смартфона и быстро его получить, в чем роботы уже заменили людей и какие еще инновации ждут нас в будущем?
Liga.Tech исследовала, как функционирует и работает современный автомобильный завод изнутри.
Историческая справка
Как работают сборочные линии автомобилей
Появление линий по производству автомобилей привело к революции в автомобильной промышленности, а также в американской жизни. Они сделали производство автомобилей более эффективным. Благодаря этому себестоимость производства автомобиля снизилась, а после этого упала и розничная цена автомобилей. Более доступные цены позволили большему количеству людей купить собственное транспортное средство.
Первые автомобили преимущественно строили производители карет. Первые автопроизводители покупали двигатели у производителя и устанавливали их в модифицированные конные кареты.
Вскоре производители кузовов обнаружили, что могут производить больше автомобилей быстрее, если стандартизируют конструкцию и детали. Вместо того чтобы производить каждую деталь в каждом автомобиле, все компоненты транспортного средства можно было производить с помощью форм и машин. Затем рабочие просто собирали готовый продукт.
Читайте такжеВ Украине заработали новые правила продажи б/у авто: власти ожидают до 60 млрд грн налогов
Кто первым использовал автоматизированную сборную линию
Первую современную сборочную линию создал не Генри Форд. На самом деле ее изобрел Рэнсом Эли Олдс (основатель автомобильной компании Oldsmobile). Олдс работал над автомобилями большую часть своей жизни, включая автомобили с паровым двигателем в 1880-х и 1890-х годах.
Его сборная линия позволила ему стать первым массовым производителем автомобилей в Соединенных Штатах, и он доминировал в американской автомобильной промышленности с 1901 по 1904 год. Бренд просуществовал с 1897 по 2004 год.
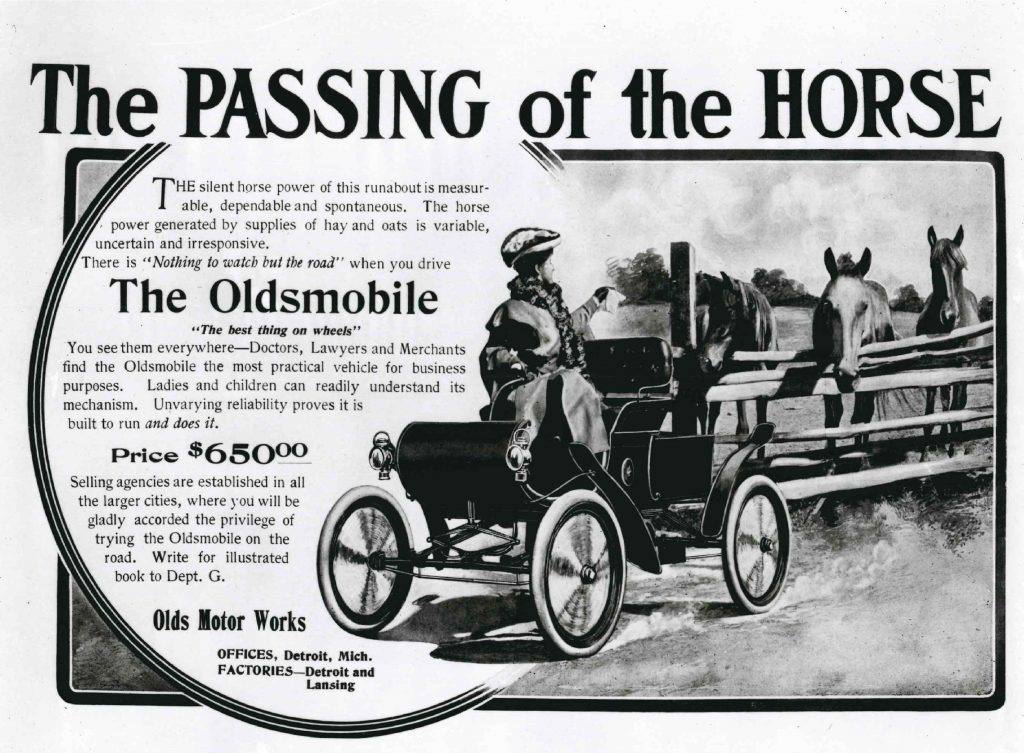
Генри Форд усовершенствовал эту идею и весь процесс заработал гораздо эффективнее, что позволило снизить стоимость производства автомобилей. Достиг он этого очень просто: каждый сотрудник выполнял одну и ту же задачу на каждом транспортном средстве. Это значительно снизило цены на новые машины и открыло доступ людям, которые раньше не могли позволить себе такую роскошь.
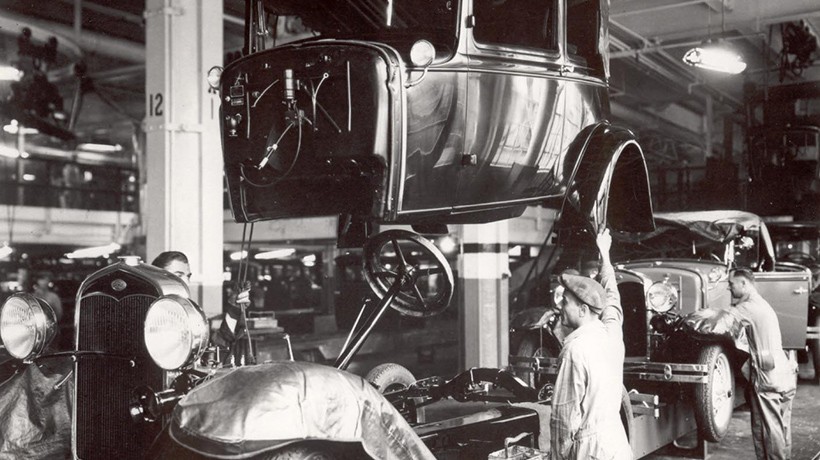
Современная производственная линия
Что поражает в современной работе сборочной линии, это то, что она не слишком отличается от базовой системы Ford, которая существовала более 100 лет назад. Автомобили по-прежнему поступают к рабочим на отдельные рабочие станции, каждый рабочий выполняет определенную задачу, и когда все задачи выполнены, в конце линии вы увидите совершенно новые готовые автомобили, сходящие с конвейера.
На современных производственных линиях многие детали, идущие на сборку автомобиля, не производятся на месте. Эти детали (например, тормозные диски или трансмиссию) покупают у других компаний-поставщиков, многие из которых имеют собственные сборочные линии.
Один из ключей к производственной линии автомобиля – стандартизация продукта.
Автомобильная платформа как элемент стандартизации
Чтобы оставаться в бизнесе сегодня, автомобильным компаниям необходимо предлагать множество разных моделей – а это трудно сделать, когда вы зависите от производственной линии.
Поэтому автомобильные компании делают то, что называется совместным использованием платформ. Это позволяет разрабатывать свои автомобили с учетом взаимозаменяемых деталей, экономит деньги, упрощает производство и по-прежнему дает потребителям то, что они хотят.
В качестве примера можно привести платформу MQB концерна Volkswagen AG (VAG), лежащую в основе огромного количества моделей всех марок производителя: от VW и Audi до более доступных Seat и Skoda.
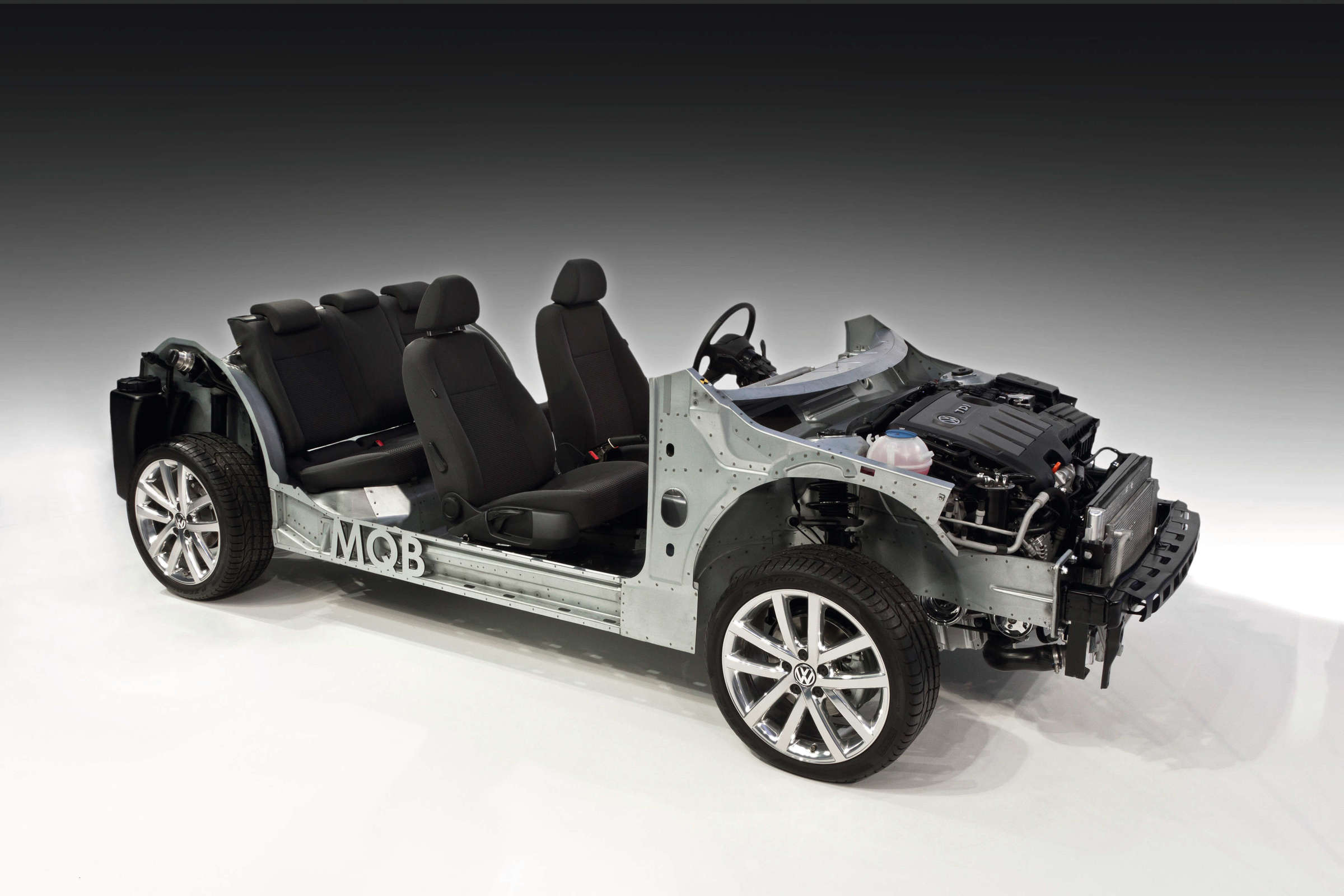
Для электромобилей в VAG разработана отдельная платформа MEB. Все современные электромобили компании сделаны именно на этой платформе.
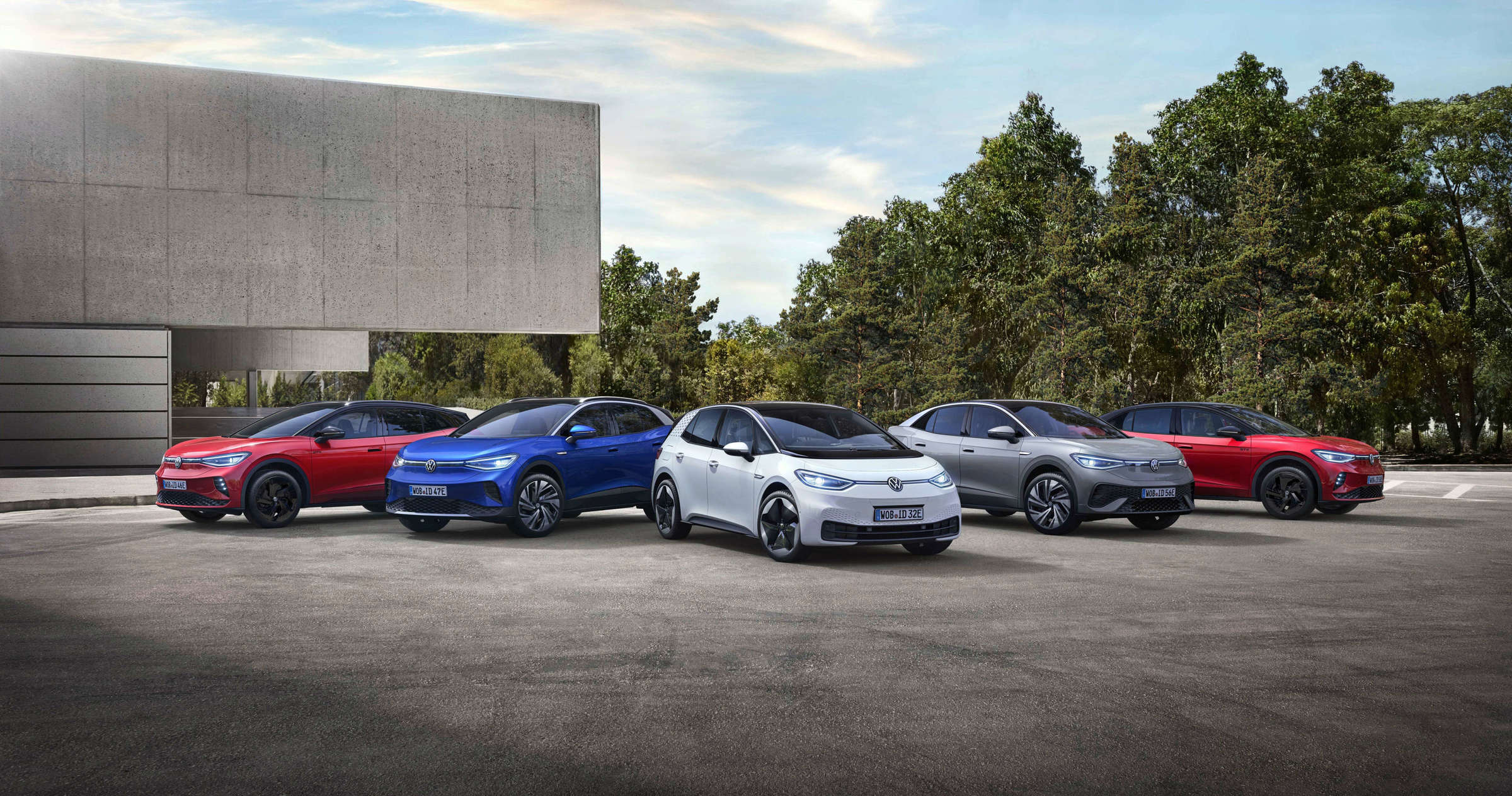
Хотя основные принципы работы автомобильных производственных линий остались неизменными, недавние инновации несколько изменили ситуацию. Теперь вместо людей работают роботы, особенно там, где работа предполагает повторяющиеся движения. К примеру, этот процесс мы можем увидеть на заводе Hyundai.
Читайте также"Привет" для Путина и Кима. Как южнокорейские Hyundai и LG могут вооружить Украину
Завод Hyundai: роботы и ИИ на службе человека
Процесс покупки автомобиля практически не изменен в течение десятилетий, но с появлением электромобилей произошли изменения. К примеру, Tesla продает машины через свой сайт, а не через традиционных дилеров. Hyundai пошел еще дальше. Так, на его заводе вы можете заказать автомобиль с помощью смартфона и выехать на нем за считаные часы!
Инновационный центр Hyundai Motor Group в Сингапуре (сокращенно HMGICS) – это не просто обновление традиционной сборочной линии. Это футуристический взгляд на наше все более роботизированное будущее, управляемое искусственным интеллектом.
Площадь HMGICS – 86 900 кв. м, завод работает с начала 2023 года и производит около 30 000 электромобилей в год. Здесь собирают IONIQ 5 и полностью автономные роботакси IONIQ 5 и IONIQ 6.
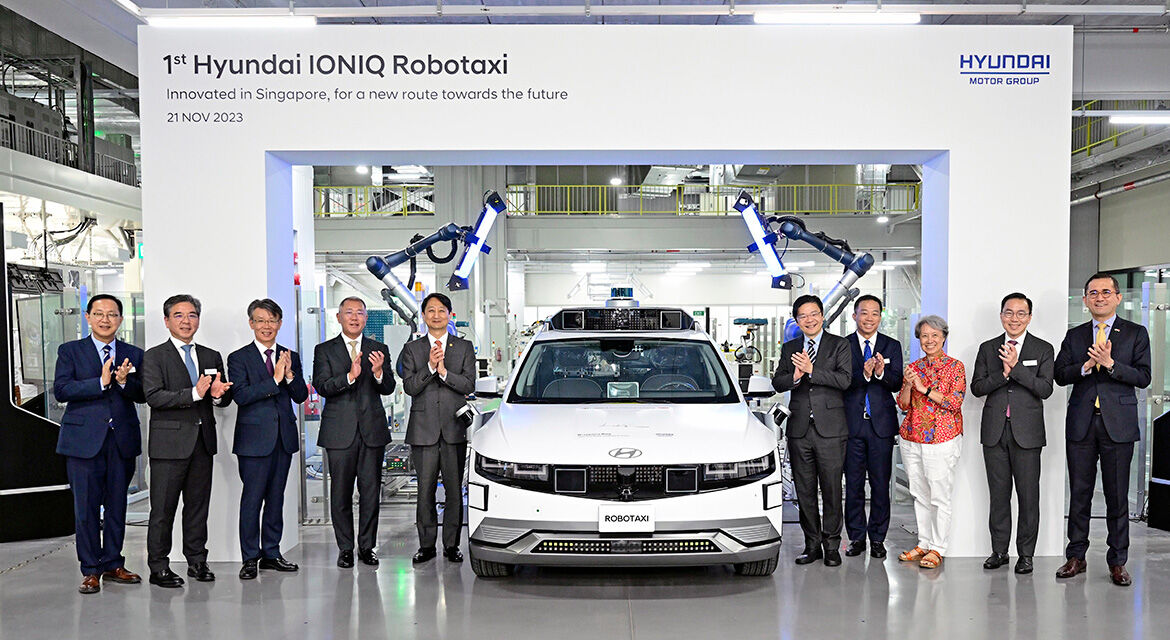
HMGICS не похож на ни один завод по производству автомобилей для массового рынка.
Приблизительно 50% всех задач выполняют 200 роботов, причем люди, робототехника и системы искусственного интеллекта достигают беспрецедентного уровня сотрудничества. Добро пожаловать на завод будущего!
Роботы выполняют сборку, проверку и организацию производства, а также заботятся о более чем 60% управления процессами компонентов, заказа и транспортировки. Это освобождает людей от повторяющихся и трудоемких задач, чтобы сосредоточиться на более творческих и продуктивных обязанностях.
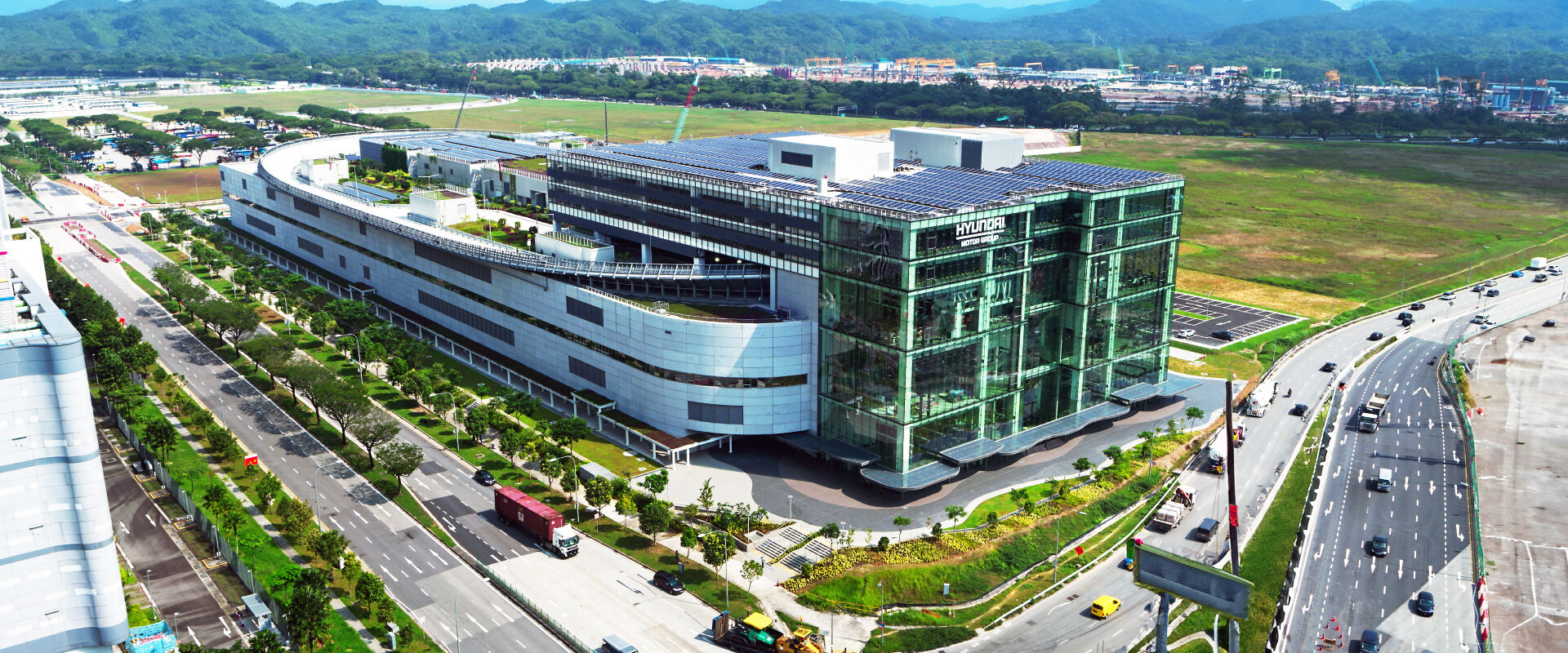
В настоящее время на "заводском этаже" работает всего 29 сотрудников. Люди работают вместе с роботами и даже отчитываются им. Контролем качества продукции компании занимается Spot – ловкий робот-пес от Boston Dynamics.
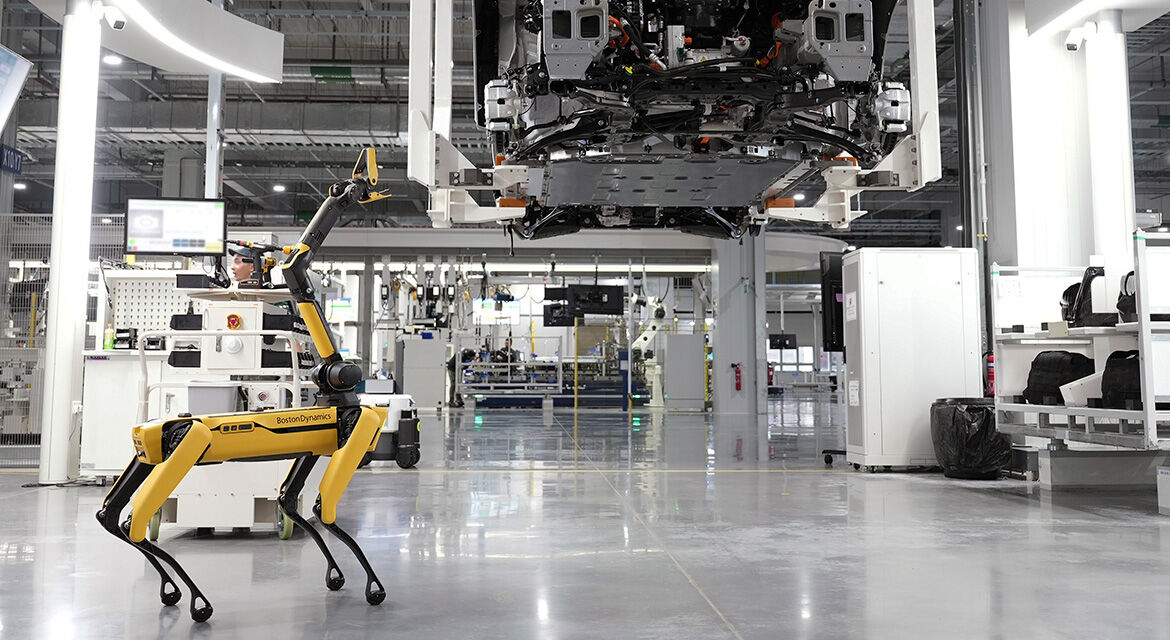
Spot регулярно выезжает со своей зарядной станции для проверки качества сборки соответствующего авто. С помощью передовой камеры, датчика и технологии искусственного интеллекта, он сканирует транспортное средство на предмет неполадок, а затем сообщает о результатах оператору из командного центра, контролирующего весь процесс.
В случае, когда Spot (и командный центр) удовлетворены качеством работы, инженер может продолжить работу над автомобилем.
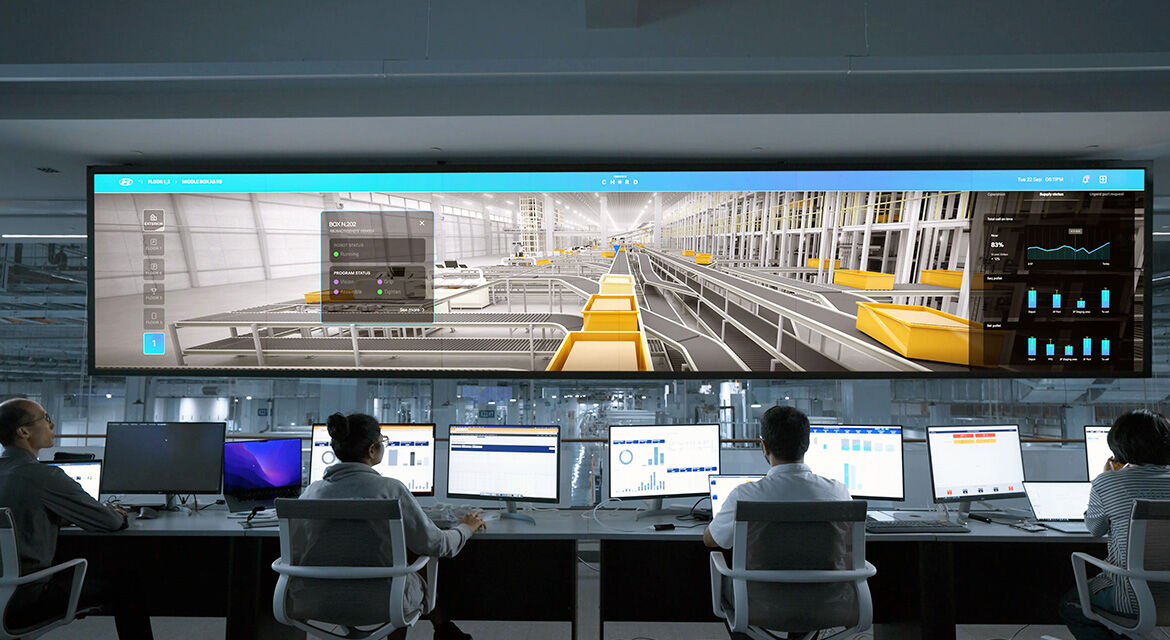
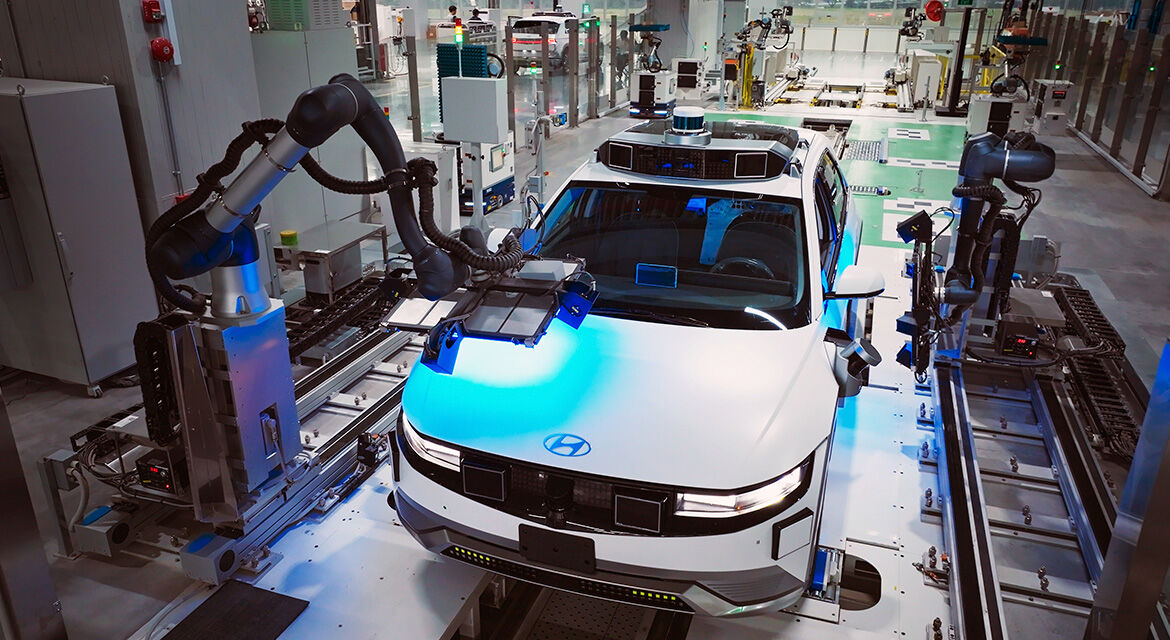
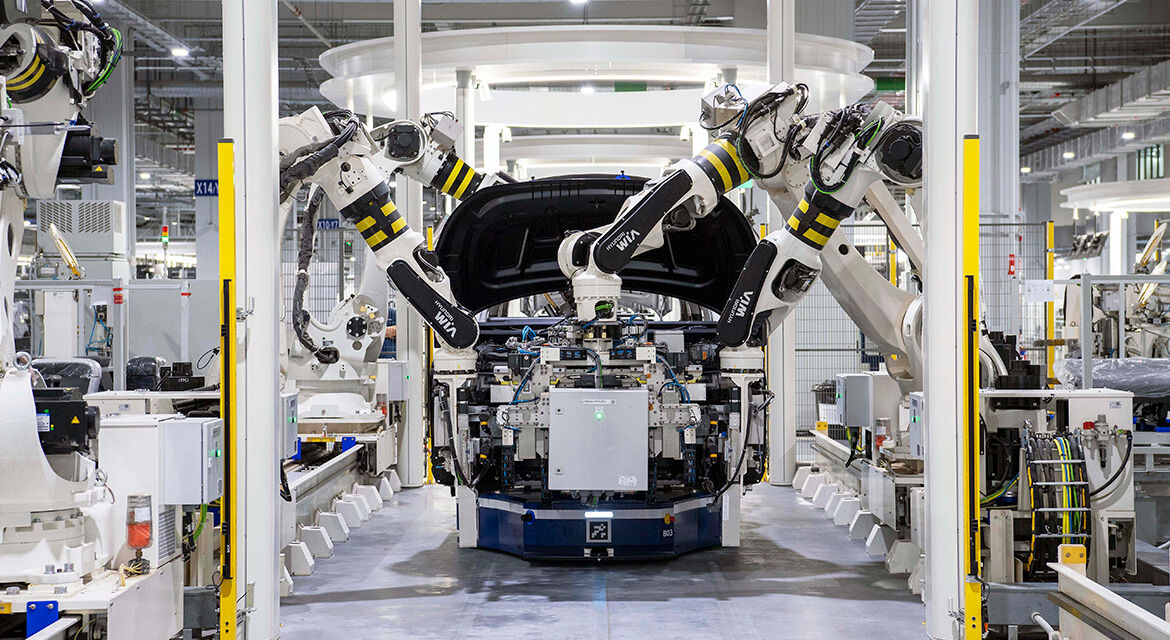
Руководитель Smart Factory Алпеш Патель в комментарии Bloomberg рассказывает об уникальном предложении для потенциальных состоятельных клиентов. "Они смогут заказать автомобиль дистанционно, выбрать цвет и даже высокоперсонализированные элементы для своего автомобиля, а затем стать свидетелями того, как он производится", – говорит он.
Патель утверждает, что с момента заказа автомобиля клиентом до его отправки может пройти всего три часа благодаря уникальной организации высокоавтоматизированного производства.
Также клиенты могут пройти тест-драйв на потрясающей 618-метровой трассе Skytrack на крыше завода.
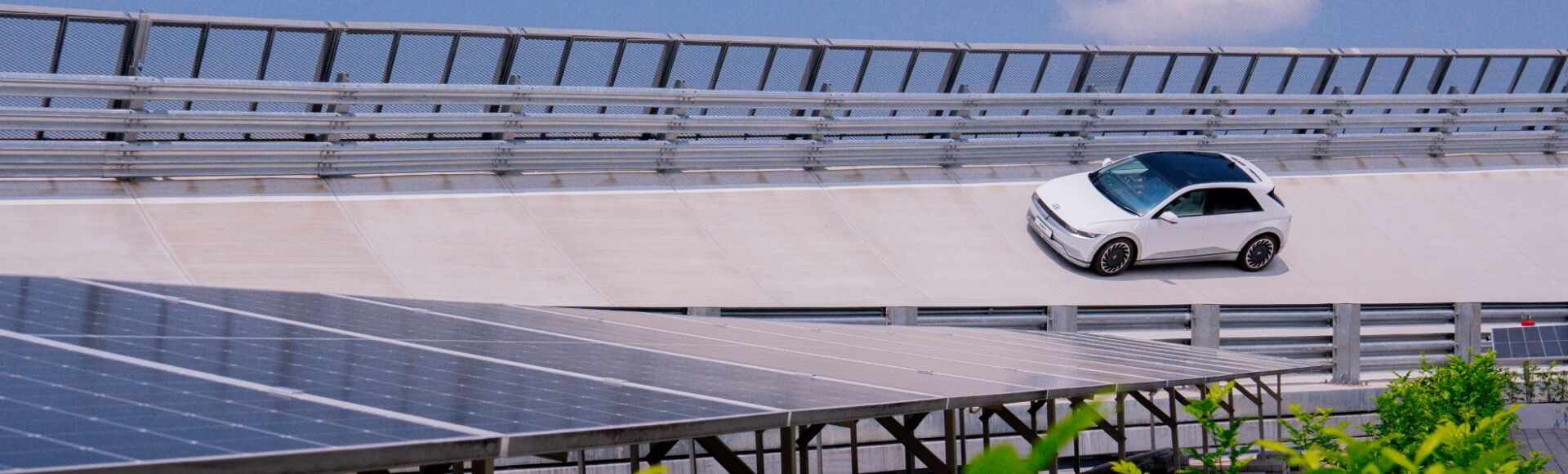
Как производится Porsche: один из самых современных заводов в мире
Завод по сборке автомобилей Porsche AG в Лейпциге ведет свою историю с 2002 года. Здесь производят самую популярную модель Porsche – кроссовер Cayenne и флагмана модельного ряда компании – премиальное купе Panamera и электрический Macan. В конце 2023 года новая Porsche Panamera Turbo E-Hybrid стала двухмиллионной машиной лейпцигской сборки.
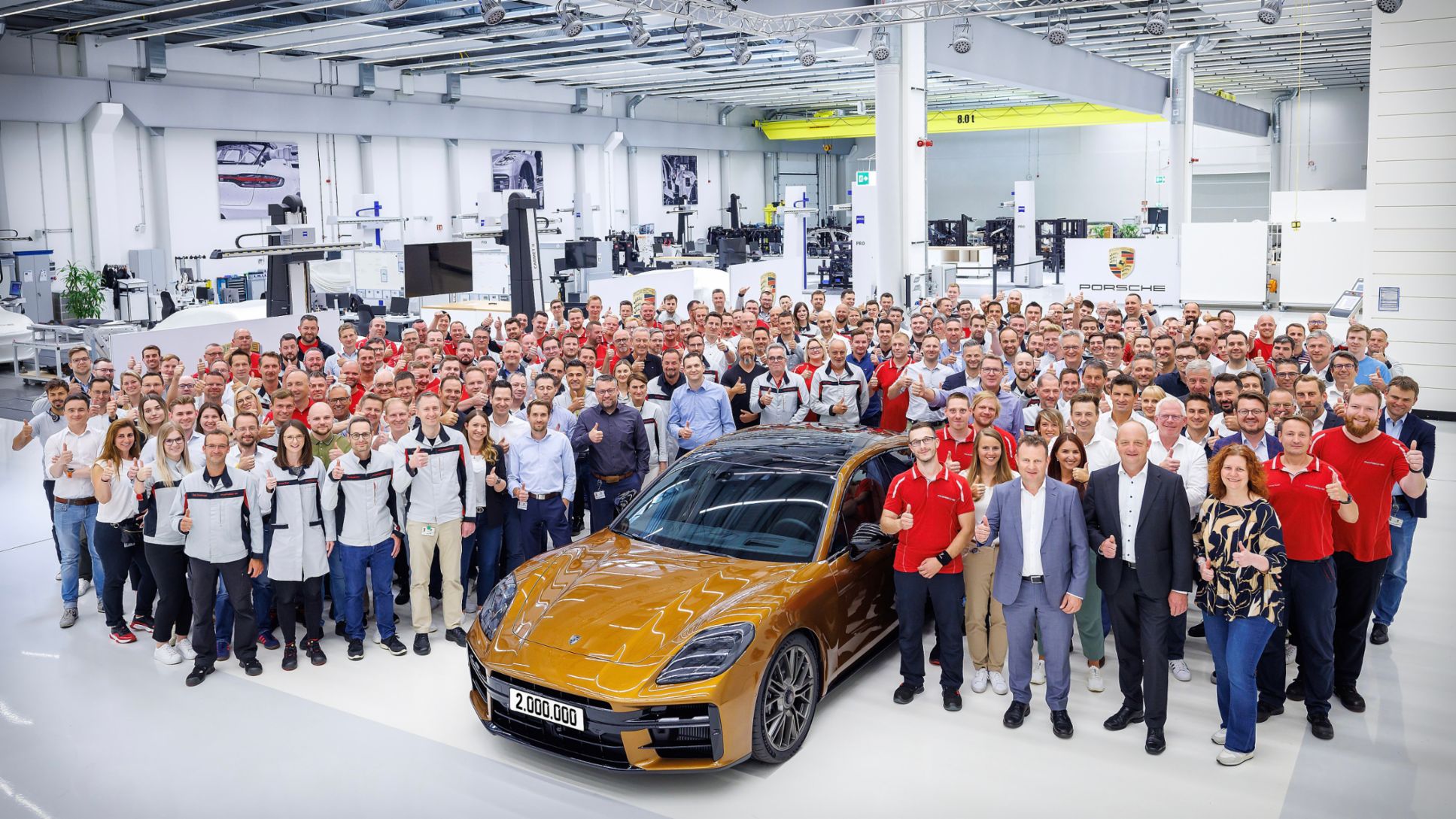
Кузовной цех
На заводе Porsche в Лейпциге есть три кузовных цеха: один для Macan с ДВС, один для Panamera и один для электрического Macan. Сначала машина получает табличку с VIN-номером (по нему можно узнать все детали и характеристики автомобиля) и другие маркировочные таблички, которые крепятся на подструктуру кузова.
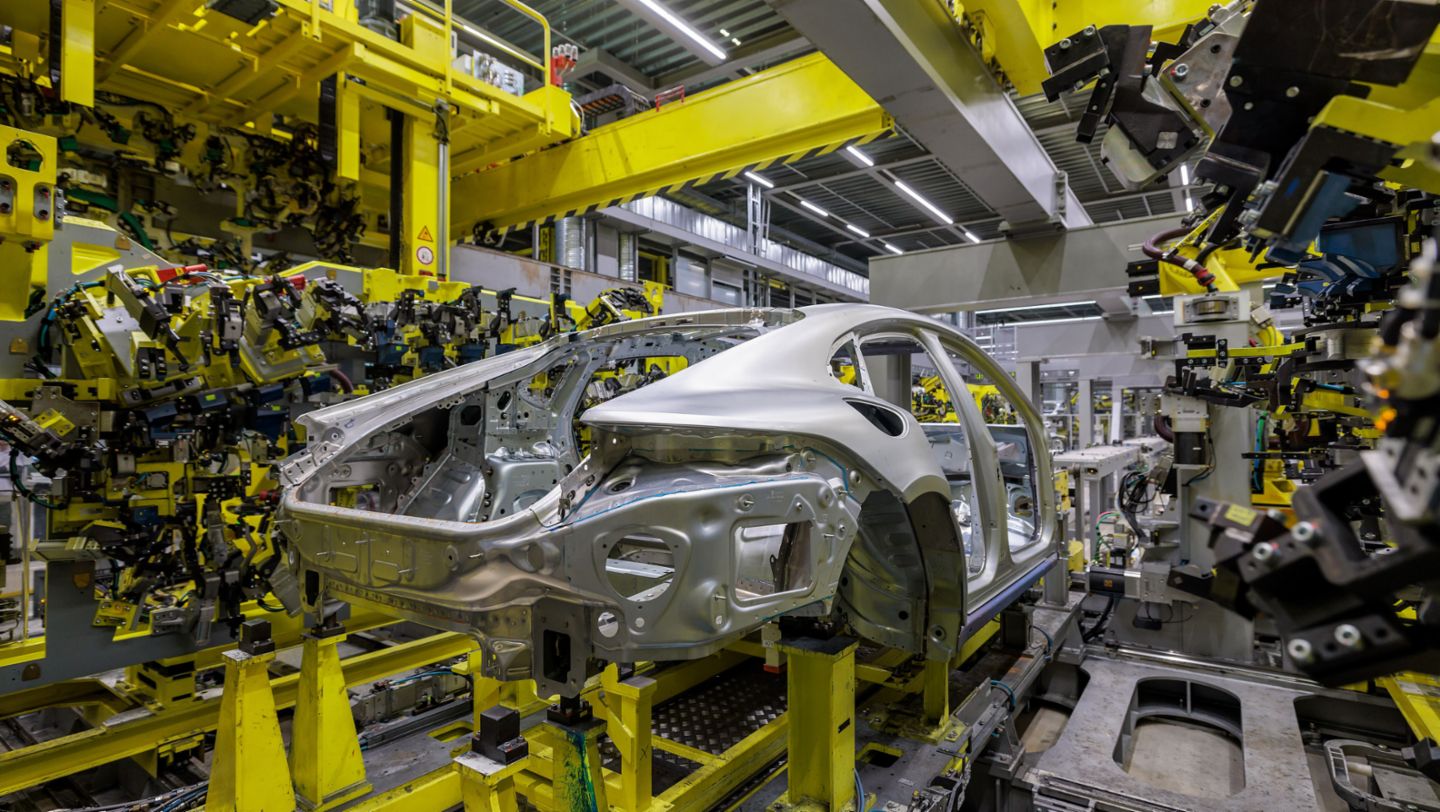
На следующем этапе боковины и крыша крепятся к подструктуре. Затем на каркас кузова устанавливают двери, капот и заднюю крышку. На финальной прямой автомобиль проходит проверку качества. Здесь, например, рабочие тщательно проверяют швы, клеевые соединения и качество поверхности. Если все требования к качеству соблюдены, кузов передают в покрасочный цех.
Покрасочный цех
Сначала кузов очищают, обезжиривают и погружают в раствор фосфата цинка, обеспечивающего оптимальную адгезию дальнейшей защиты от коррозии. Также герметизируют швы и наносят три разных слоя краски: грунтовка, финишное покрытие и прозрачное покрытие. Эластичная грунтовка защищает финишное покрытие (также известное как базовое покрытие) от повреждений и улучшает структуру и последующий блеск. Затем наносят финишное покрытие в цвете, выбранном заказчиком. После промежуточной сушки прозрачный лак запечатывает нанесенные ранее слои краски.
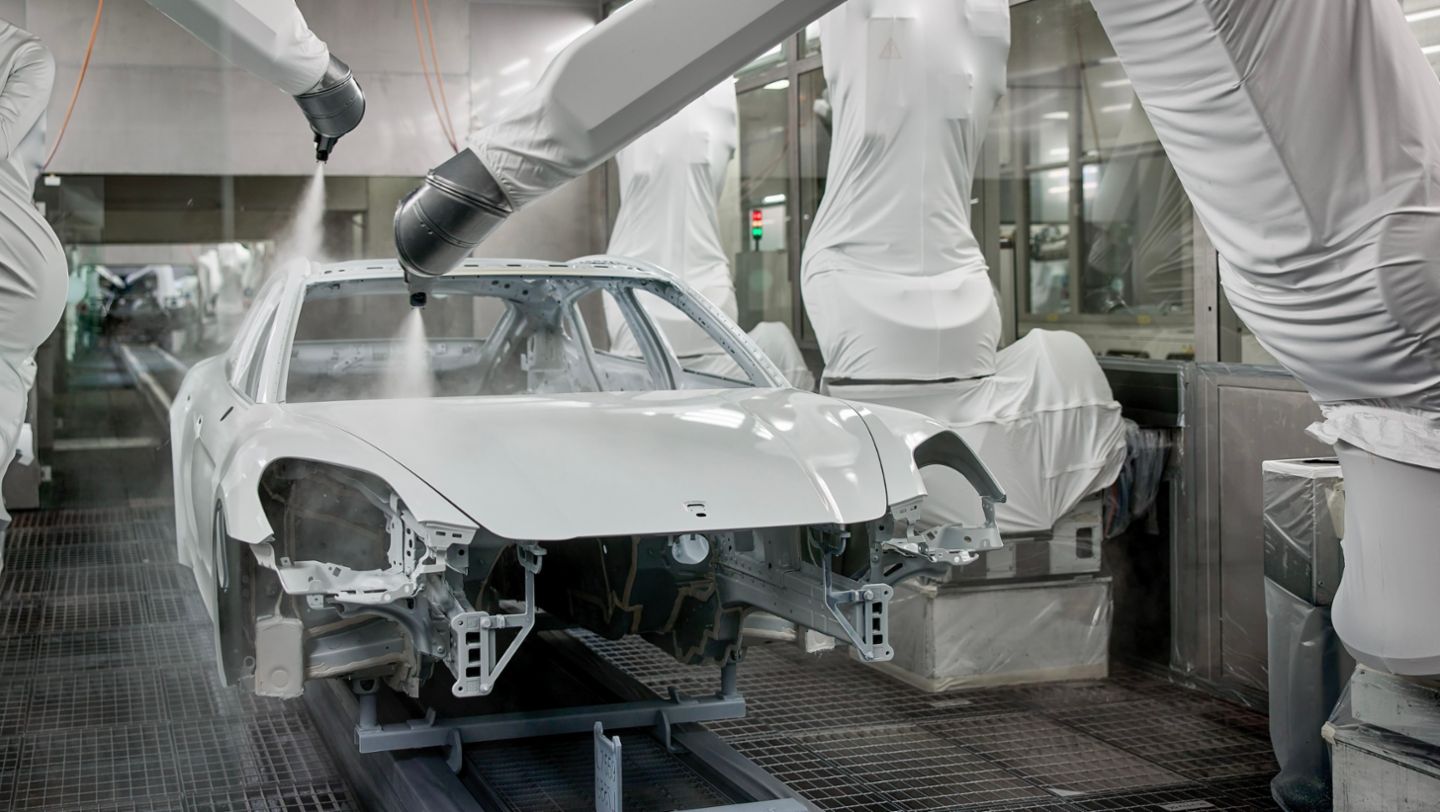
Все окрашенные кузова проверяют рабочие в светодиодном световом тоннеле. Дополнительную поддержку обеспечивает автоматизированная система обнаружения ошибок (AFE). За 70 секунд два робота сканируют всю наружную поверхность кузова с помощью шаблона из световых полос. В процессе они производят около 100 000 фотографий. В течение следующих 30 секунд пять компьютеров обработки изображений оценивают результаты.
Таким образом рабочим показывают местоположение и тип обнаруженных неровновстей на 3D-визуализации кузова. Автоматизированная система обнаружения ошибок в покрасочном цехе используется в серийном производстве с 2023 года и является одним из проектов Smart Factory.
Читайте такжеHyundai из-за уменьшения спроса на электромобили решил увеличить линейку гибридов
На следующем этапе двери снимают с кузова, чтобы работать с ними отдельно. Кроме того, без снятия двери нереально установить торпеду (кабину) в салон. Macan и Panamera в зависимости от версии и комплектации кабина может состоять до 200 отдельных деталей, весить от 50 до 90 кг.
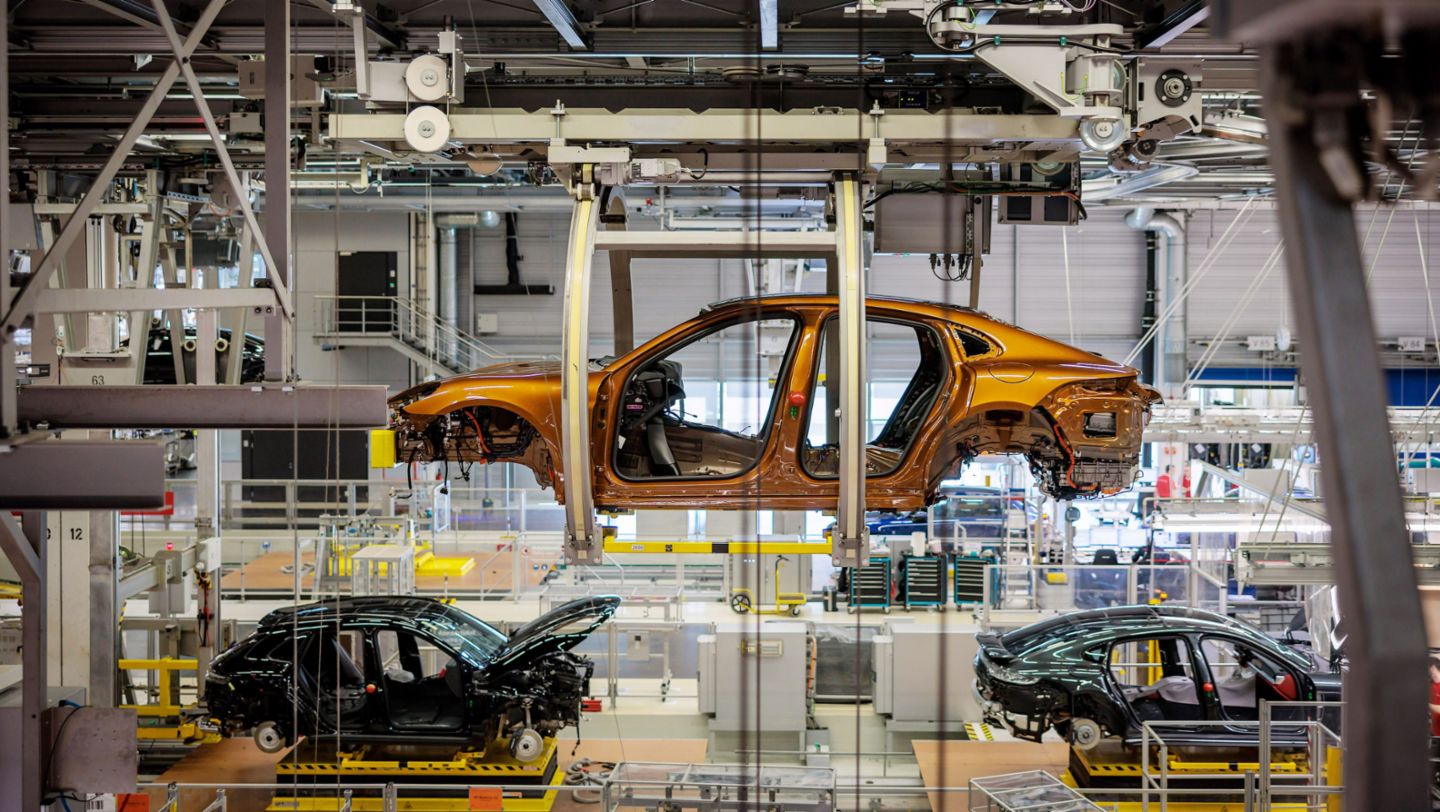
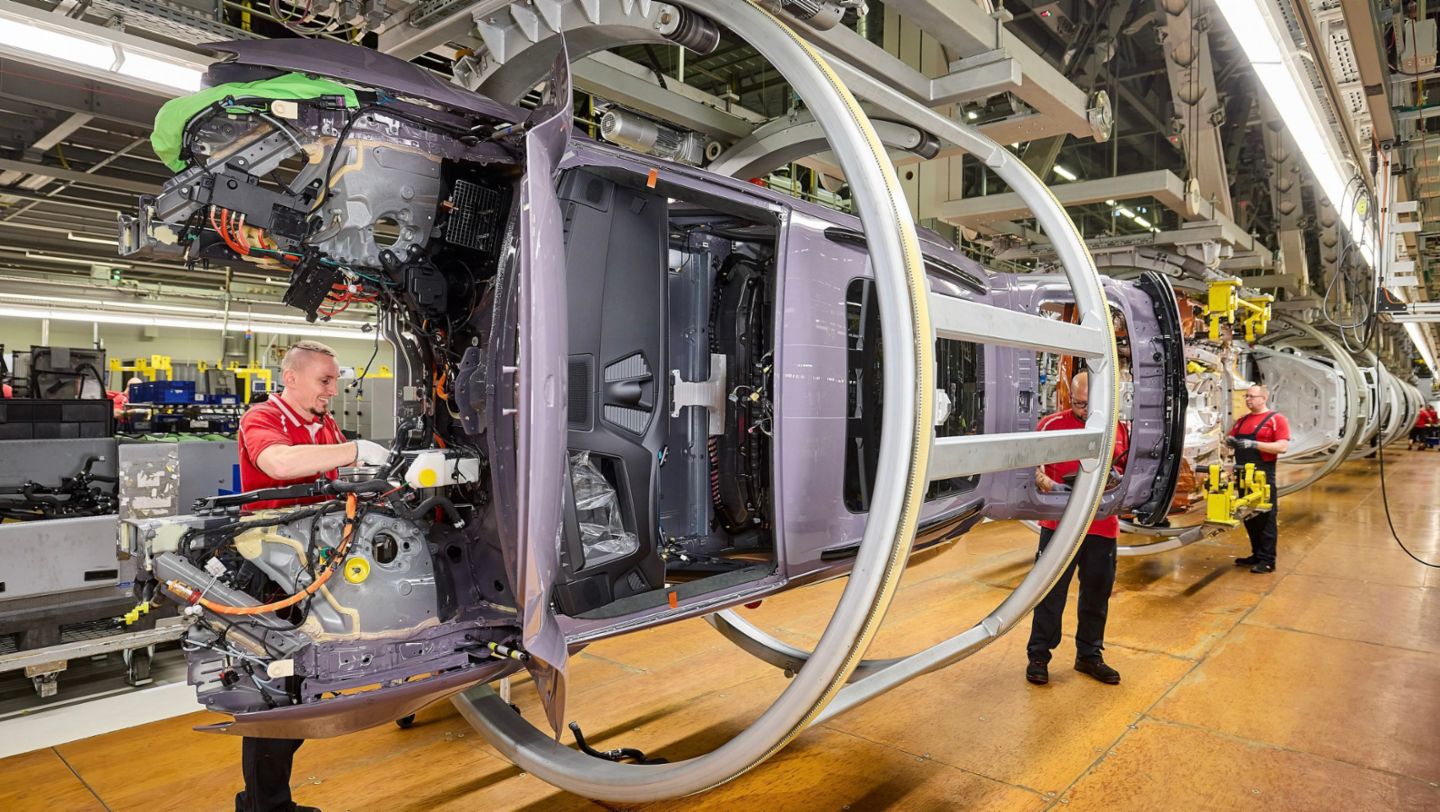
В начале процесса дверь весит около 8 кг. После процесса сборки ее вес увеличивается до 25 кг и больше.
Кстати, только длина электропроводки в Panamera – более 150 метров, а общая протяженность кабеля – около 3 километров.
Чтобы подключить все электроконтакты, нужно 4 часа. И это самая тяжелая операция на конвейере в Лейпциге. А о том, что у современных Porsche немало деталей из Украины – Liga.Tech уже писала раньше.
Другие компоненты, собираемые на этом этапе, включают сдвижные или панорамные крыши, блоки управления и обшивку крыши. Последний этап на линии сборки интерьера – "прошивка" ключа, который здесь впервые вставляется в замок зажигания.
Этап "свадьбы"
Один из важных этапов – сборка двигателей.
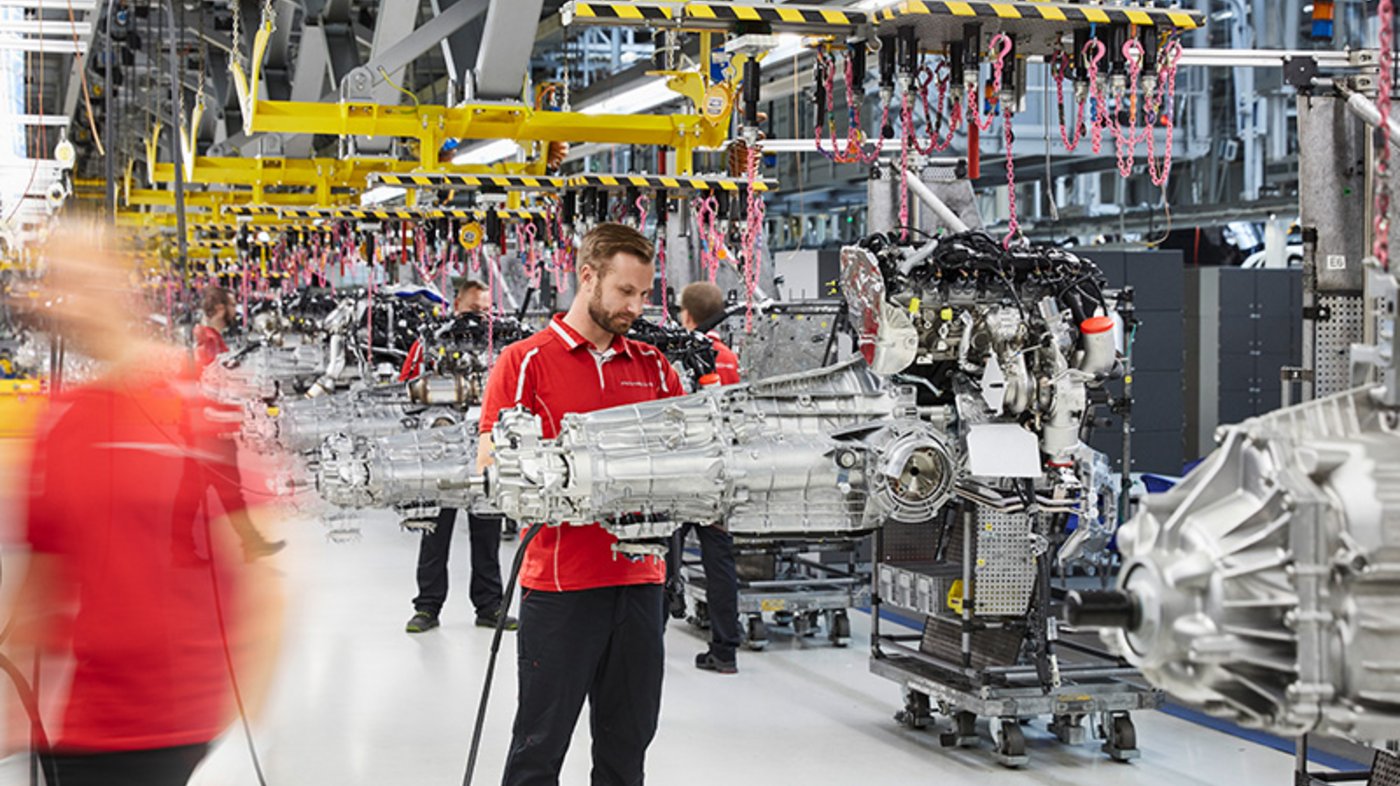
Здесь автоматизированная система управления автомобилем (AGVS) помещает готовую трансмиссию под соответствующий кузов автомобиля и крепко прикручивает ее на место. Таким образом двигатель, шасси и кузов фактически "вступают в брак". На последнем шаге инсталлируются выхлопные трубы.
Среди подключаемых на этом этапе систем – тормозные магистрали на передней и задней осях, топливные трубки и компоненты воздуховода для пневматической подвески; заливаются все нужные жидкости. На машину устанавливают колеса.
Тестовая линия
Происходит первый запуск двигателя, окончательная настройка шасси и фар, а также калибровка систем помощи водителю. После завершения этих шагов автомобили отправляются на динамометрический стенд для моделирования вождения на максимальной скорости 120 км/ч на общую дистанцию 1,5 км.
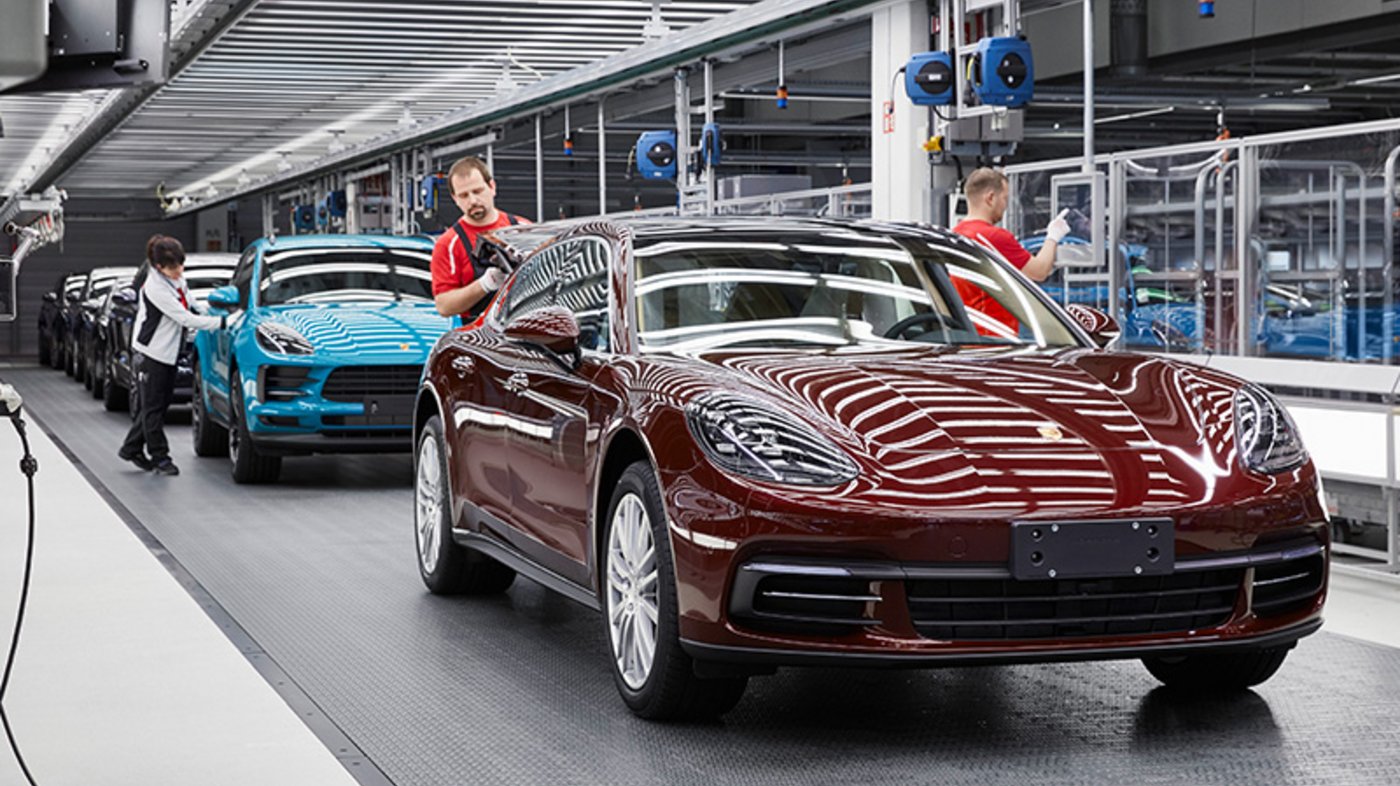
Во время окончательной проверки качества машину тестируют на испытательном треке. Проверяют освещение, водонепроницаемость кузова. После этого каждый Porsche отправляют в моющий бокс, где проходит полную чистку. После дополнительных проверок качества, автомобиль наконец-то выпускают и упаковывают для транспортировки.
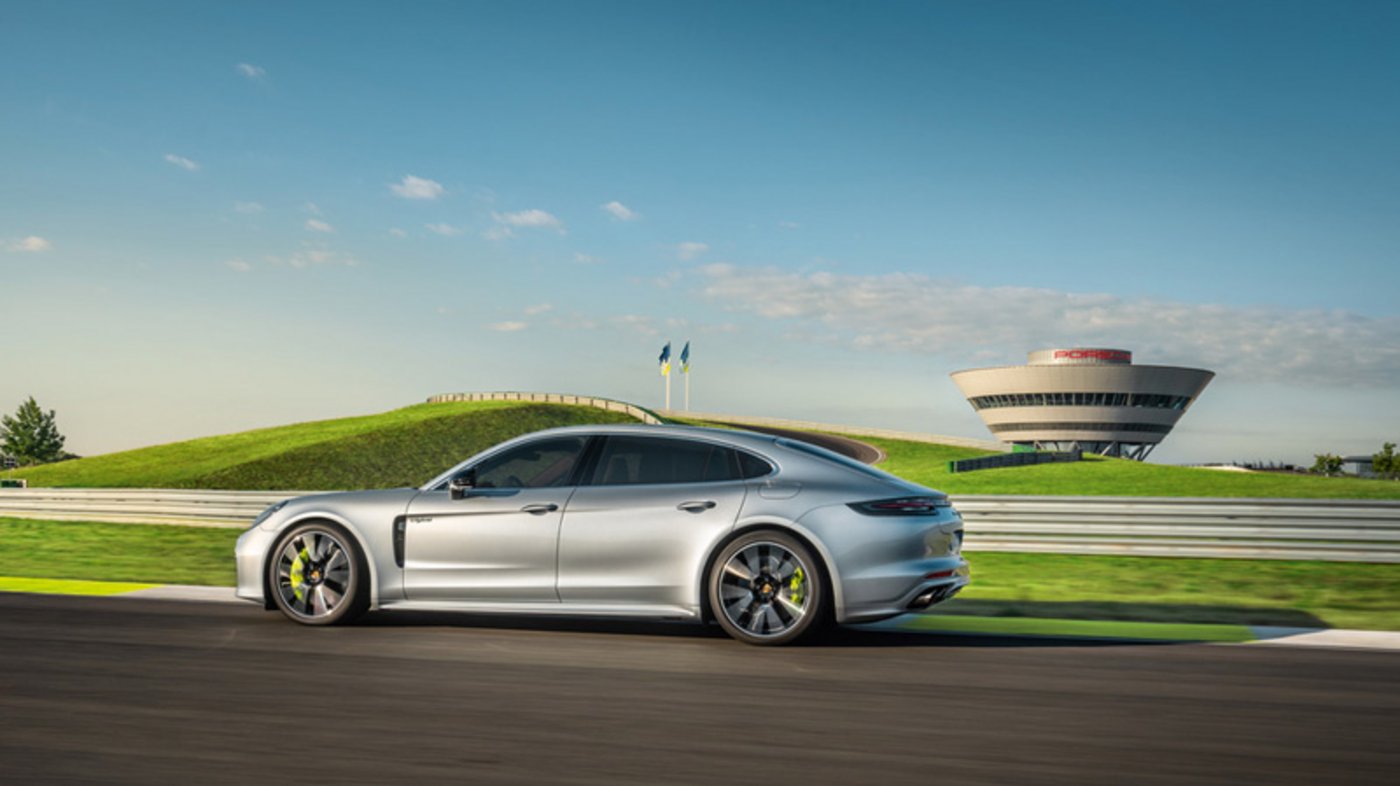
Как производят электромобили: самое интересное о Fiat 500 electric
Открытый в 1939 году завод Mirafiori в Турине ознаменовал начало современного производства Fiat и остается одним из старейших автомобильных заводов в Европе. Площадь более 2 млн кв. м, около 12 км подземных дорог для транспортировки двигателей и компонентов и более 20 км транспортных систем для перемещения материалов и готовых автомобилей.
Fiat 500 образца 2007 года уже скоро будет снят с производства из-за более жестких правил ЕС в области кибербезопасности и электроники. Поэтому еще в конце 2020 года завод модернизировали и здесь начали производить электрическую версию обновленного Fiat 500.
Читайте такжеVolkswagen закроет два автозавода в Германии, чтобы сократить расходы
Завод Mirafiori долгое время являлся местом рождения гениальных идей и футуристических проектов. Здесь выпускали знаковые модели, вошедшие в историю автомобилестроения, стимулировали развитие технологий и во многих случаях даже сопровождали изменения в итальянском обществе.
Первым был легендарный Topolino, самый маленький серийный автомобиль в мире. Затем появился 600, первый народный автомобиль в Италии, который спустя несколько месяцев на рынке пользовавшийся таким большим спросом, что очередь на его получение растянулась на год. Также стоит упомянуть Fiat 500, выведший Италию на дороги после Второй мировой войны, ставший аккомпанементом экономического развития.
Затем настал черед безудержной Panda (выпущено более 7,5 миллионов ед.). Здесь выпускалось немало знаковых для Италии моделей: кроме Fiat, собирали Alfa Romeo, Lancia и даже Maserati.
Помимо производства авто, компания вкладывается в образование – один из кампусов Политехнического университета Турина находится в Мирафийоре, на Корсо Сеттембрине: это цитадель дизайна и устойчивой мобильности. Об украинских автодизайнерах, которые здесь учились, Liga.Tech уже писала раньше.
Как работает завод Mirafiori: инновации, роботы
В проект инвестировано более 700 миллионов евро, около 1200 человек работают исключительно над производством 500 electric.
Под эту модель создана специальная производственная линия, которая даже использует дополненную реальность для улучшения продукта и процессов. "Система производства" (MES) предоставляет возможность отслеживать заказы клиентов и заранее отправлять эти данные внешним поставщикам.
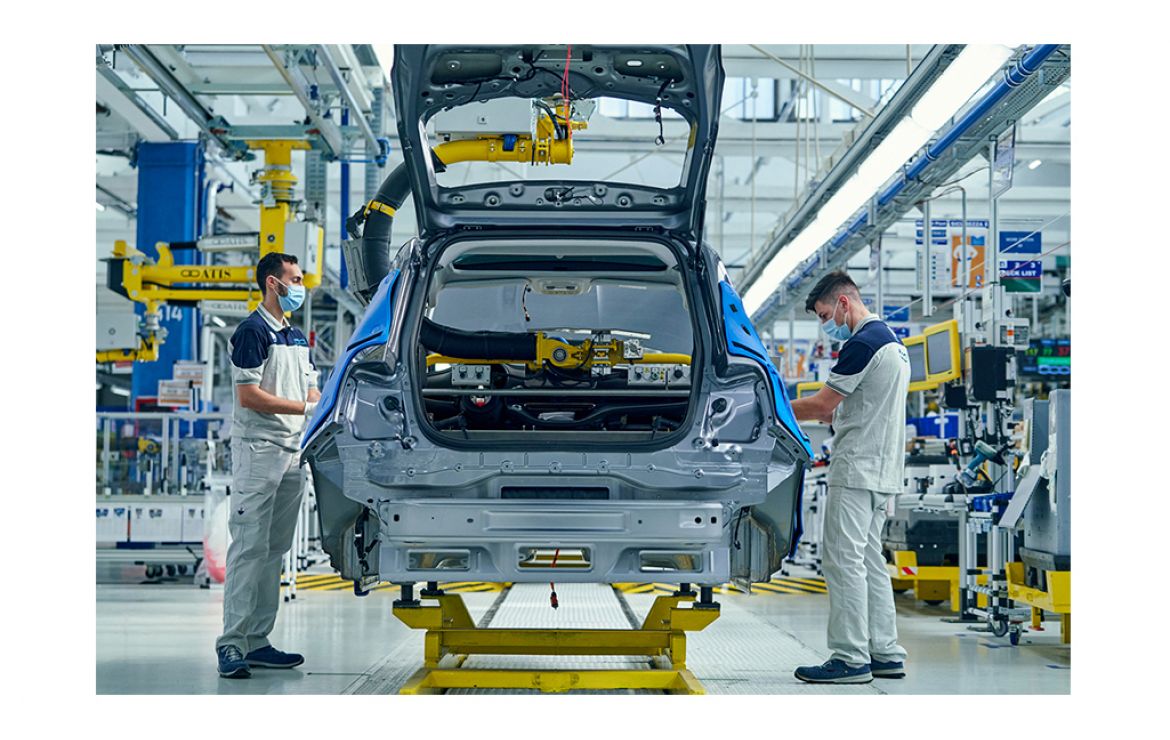
Система также упорядочивает детали перед отправкой их на производственную линию, поэтому работники получают нужную деталь именно тогда, когда она им нужна.
Руководитель координирует группу сотрудников и отвечает за их обучение. Люди в этой должности руководят небольшой частью процесса, контролируя качество и производство. В работе каждый руководитель группы поддерживается технологиями. Из интересного – все выполненные задания регистрируются в ИТ-системе, с помощью которой руководитель группы может проверять и подтверждать результат каждой из них на мониторах рядом с производственной линией или на своем смартфоне.
Процесс сборки нового 500-го начинается на "линии комплектации". Это первая точка, которой новая модель достигает в процессе сборки после покраски. Работа начинается с разборки дверей, подготовленных на специальной линии, где одним из самых интересных процессов является прокладка гидроизоляции. Там робот занимается ламинированием, обеспечивая самые высокие стандарты качества.
Это первый случай, когда Fiat Chrysler Automobiles (с 2021 года – Stellantis) использовала горячекатаные рулоны для гидроизоляции автомобиля. Затем происходит процесс прокладки кабелей, приборной панели и центральной консоли. После завершения процессов trim line в автомобиль устанавливаются приборная панель и центральная консоль.
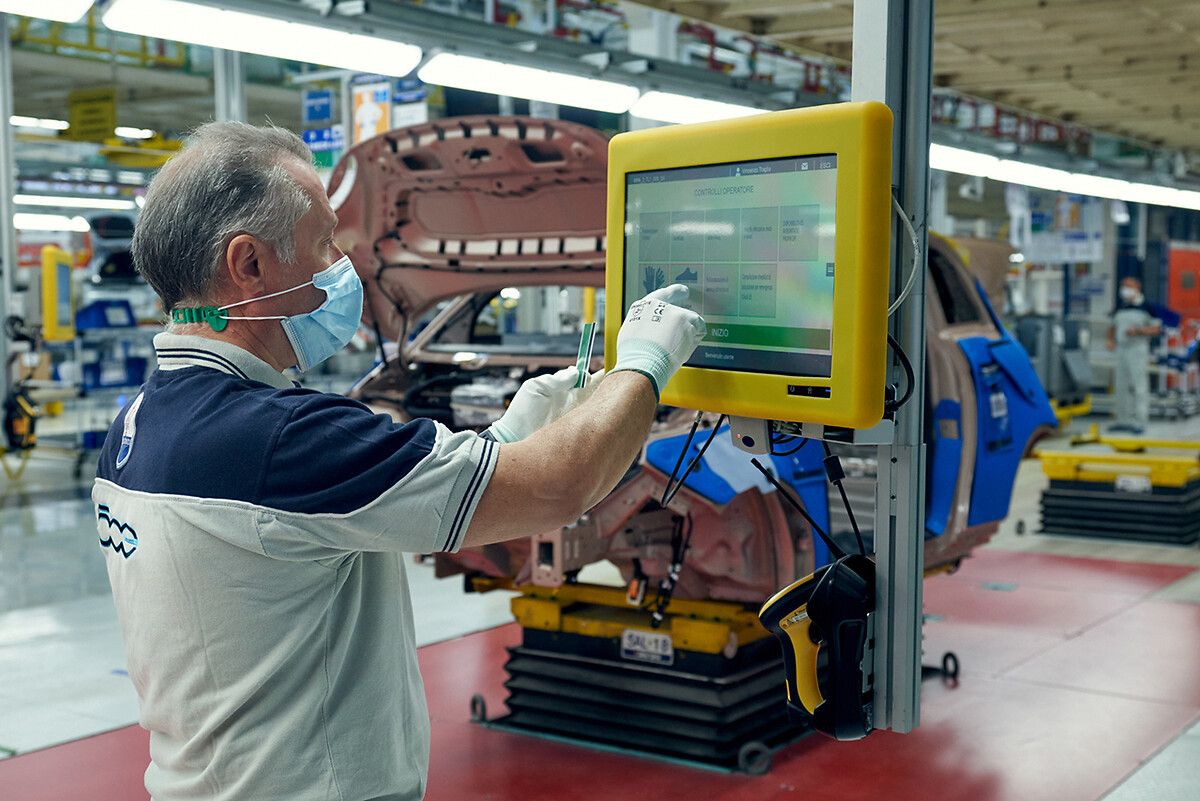
Одна из особенностей производства – операторский терминал, монитор на каждой рабочей станции, который предоставляет данные по сборке на каждом этапе. Нажав на экран, они могут подтвердить качество, запросить материал и связаться с руководителем группы для решения проблемы.
Если руководитель группы не может решить проблему до того, как транспортное средство покинет рабочую станцию, линия автоматически останавливается, чтобы предотвратить возникновение неисправностей.
Еще одна новая функция, внедренная с производством нового Fiat 500, представлена в зоне "Вклеивание окон", где робот устанавливает лобовое и заднее стекло с высокими стандартами качества.
Это местоположение первого лазерного инструмента, установленного FCA, для обжига номера шасси. По сравнению с обычными технологиями, это небольшое оборудование обеспечивает лучшую обработку, большую точность и не производит шума или вибраций.
Читайте такжеЕвропейские автопроизводители теряют прибыль: акции падают из-за конкуренции с Китаем
Этап "свадьбы" между двигателем и днищем. Одним из инновационных элементов является прокладка кабеля зарядки аккумулятора. Пока одна группа рабочих собирает шасси, другая группа готовит механические компоненты, устанавливая колесные узлы и органы управления электродвигателем. По сравнению с обычным автомобилем основная платформа автомобиля включает аккумулятор и электродвигатель, состоящий из модуля электропривода (EDM) и отсека электропитания (PEB).
Другие важныеи компоненты – электрический нагреватель воздуха и компрессор. После завершения тяговой системы все готово к ее сборке с кузовом: "свадьба" выполняется автоматически. Затем основная платформа транспортируется более гибким автоматическим транспортным средством с индукционным приводом, разными скоростями которого можно легко управлять.
Следующий этап для электрического 500-го – сборка дверей, сидений и рулевого колеса, все это происходит на рабочих станциях со строгим контролем качества.
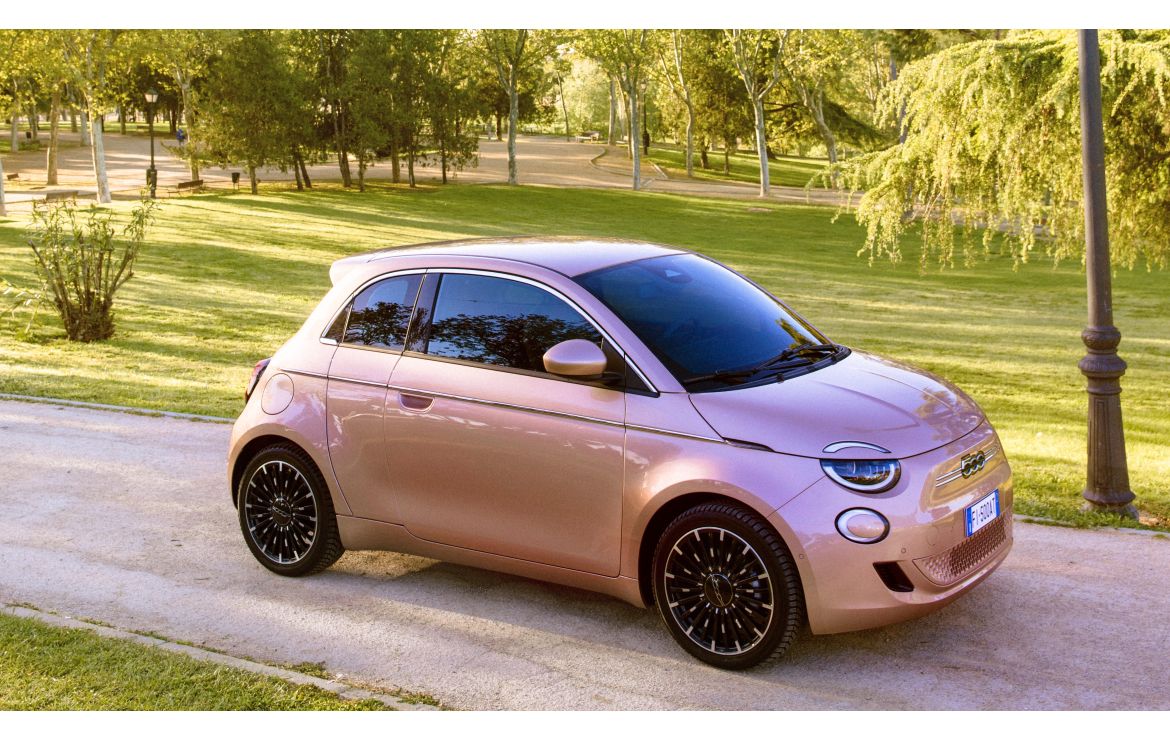
Из-за низкого спроса электрического 500-го в начале этого года Fiat начал выпускать и более доступную гибридную новинку Torino. В 2025-26 годах планируется выпуск еще одной гибридной новинки – Fiat 500 Ibrida, рассказал генеральный директор Fiat Оливье Франсуа.
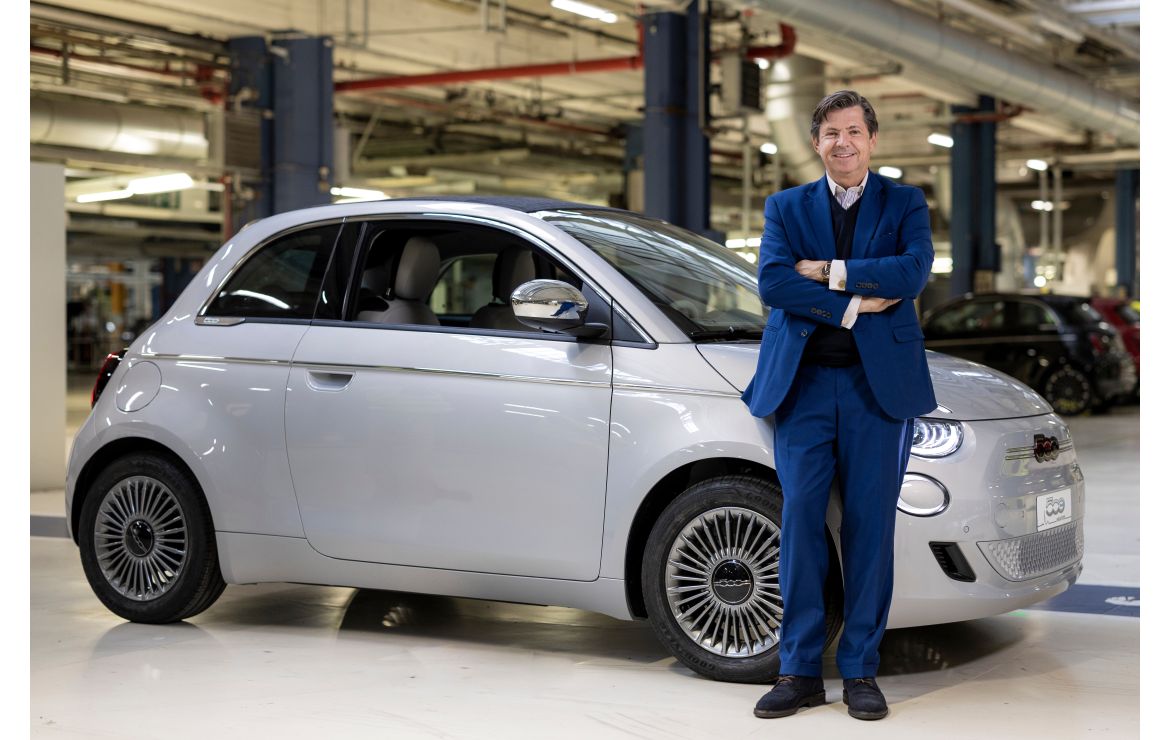
Гибридный Fiat 500 имеет не только итальянское имя, но и нарисован, разработан, настроен и сделан в Турине. ДВС для гибридов будут производить в Термоле, выпускную систему – в Неаполе, а коробку передач – на самом заводе Mirafiori.